7 Essential Tips to Streamline Your Distribution Services
- babbugabaru
- 29 minutes ago
- 3 min read
In today's fast-paced world, efficient distribution services can set your business apart from the competition. Whether you're a seasoned player or just starting out, optimizing your distribution processes is crucial for success. In this blog, we'll explore seven essential tips that can help you streamline your distribution services, improve efficiency, and enhance customer satisfaction.
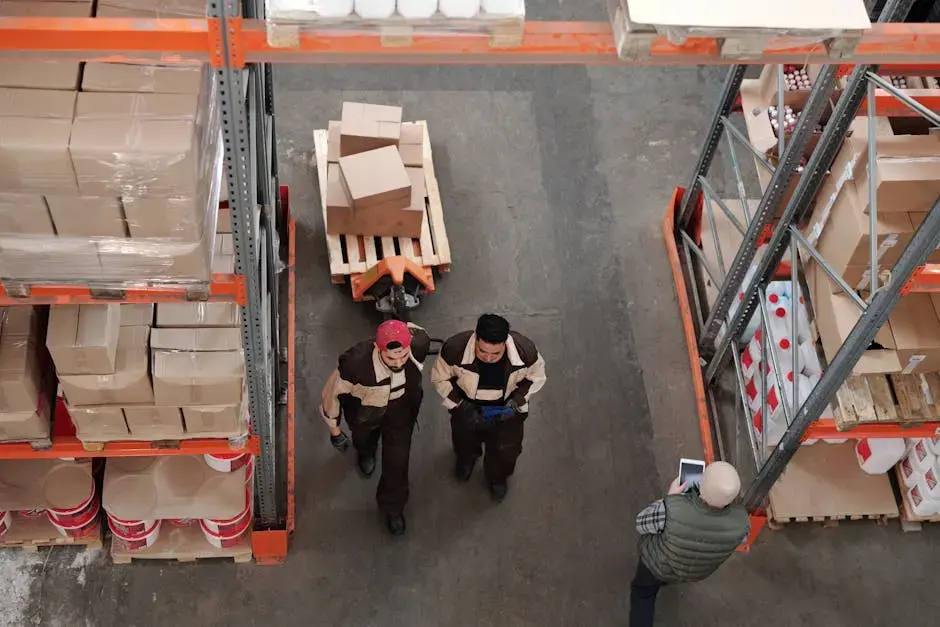
1. Assess Your Current Distribution Process
Start by taking a close look at your existing distribution workflow. Understanding the strengths and weaknesses in your current system is the first step toward improvement.
To do this effectively, consider conducting a thorough analysis of each component of your distribution process. Mapping out each stage—from order processing to delivery—will highlight areas that are running smoothly and those that may need a little extra attention.
Moreover, engaging your staff in this evaluation can provide valuable insights. Often, the employees involved in daily operations have unique perspectives on what works and what could be improved, making them essential partners in this assessment.
2. Leverage Technology for Better Management
Utilizing technology such as inventory management software can help you track shipments and manage resources more effectively. Stay updated with the latest tools that can simplify your processes.
Furthermore, employing automated systems for forecasting demand and managing stock levels not only boosts your efficiency but also minimizes human error. These systems can analyze buying patterns and predict future needs, allowing you to stay ahead of the curve.
Consider investing in a robust transportation management system as well. These platforms facilitate route optimization, which can significantly reduce delivery times and costs. The power of technology in streamlining distribution services cannot be overstated.
3. Optimize Your Warehouse Layout
A well-organized warehouse can reduce handling time and improve efficiency. Consider rearranging your layout to facilitate faster picking and packing.
Think about the flow of goods in your warehouse—products should move logically from receiving to storage to shipping. Organizing frequently picked items closer to packing stations can notably reduce travel time for staff.
Additionally, employing vertical storage solutions can maximize space, enabling you to store more inventory without expanding your facility. Revisiting your warehouse design periodically can pay off immensely in improved productivity.
4. Enhance Communication with Suppliers and Customers
Strong communication channels help ensure everyone is on the same page. Regular updates with suppliers and proactive communication with customers can significantly streamline operations.
Consider establishing a dedicated communication platform where stakeholders can share updates and feedback in real time. This transparency creates trust and ensures that potential issues are addressed before they escalate.
Moreover, engaging customers through surveys to gain insight into their distribution experience can lead to valuable improvements. Use their feedback to refine your approach and tailor services that truly meet their needs.
5. Implement Efficient Inventory Management Techniques
Incorporating practices like Just-In-Time (JIT) inventory can reduce excess stock and minimize waste, leading to a more efficient distribution cycle.
JIT inventory management requires precise forecasting and clear communication with suppliers. This approach helps in keeping inventory costs down while ensuring that products are available when customers demand them.
Consider also implementing an ABC analysis to prioritize inventory management efforts. This method categorizes inventory into three groups based on importance, allowing you to allocate resources effectively and focus on the most vital products.
6. Train Your Staff Regularly
Investing in training for your employees ensures they are well-equipped with the best practices in distribution. A knowledgeable team can increase efficiency and reduce errors.
Moreover, regular training sessions keep staff updated on the latest equipment and technologies, which can dramatically enhance productivity. Develop a culture of continuous learning where staff are encouraged to share insights and best practices.
In addition to formal training, consider mentoring programs where experienced employees guide newcomers. This hands-on approach helps in building a cohesive team that works efficiently together.
7. Monitor Performance and Seek Feedback
Tracking key performance indicators (KPIs) will provide insight into your distribution effectiveness. Additionally, don’t hesitate to seek feedback from your team and clients for continuous improvement.
Establish metrics that reflect your organization's goals, such as order accuracy, delivery times, and customer satisfaction. Regularly reviewing these metrics allows you to spot trends and make informed decisions.
Encouraging an open feedback culture can yield valuable insights and innovative solutions to challenges you may face. Remember, improvement is a collaborative effort—a motivated team is your best asset.
Comments